4th Japan Construction International Award
Construction Project Category
- Port Moresby Sewerage System Upgrading Project[Papua New Guinea]
- Design, Build, Operate & Maintain and Transfer of Salori Sewage Treatment Plant and related facilities in Allahabad[India]
- National Centre for Infectious Diseases and Centre for Healthcare Innovation[Singapore]
- Jakarta Mass Rapid Transit System (North-South Line) Project (Phase 1)[Indonesia]
- Maintenance and Rehabilitation Project of First and Second Bosphorus Bridge[Turkey]
- Noguchi Advanced Research Laboratories[Ghana]
- Tank Hill Park with Yamasen Japanese Restaurant[Uganda]

Port Moresby Sewerage System Upgrading Project[Papua New Guinea]
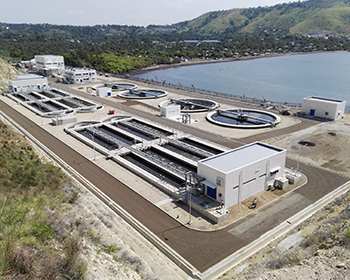

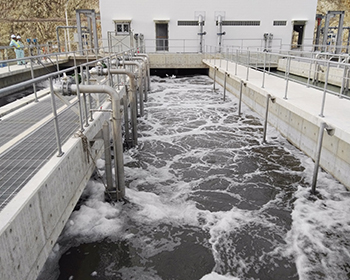

Project overview
- In this project, a full-scale large sewage treatment facility and a sewage piping network were built for the first time in Pacific island countries. The project has helped curb the outflow of untreated sewage water into to the ocean, mitigating the serious social problem of environmental destruction and preventing local residents from getting water-related diseases.
- The project was aimed to build a sewage treatment facility capable of treating 14,800 cubic meters of sewage water per day in a coastal area, along with a 1.6-kilometer ocean outfall pipe and a sewage piping network whose total length is approx. 21 kilometers (trunk: 12 kilometers; branches: 9 kilometers). It also involved repairing and constructing a total of 13 sewage pump stations. Using Japan‘s construction technology and management technique, high-quality facilities were completed safely at low cost within the construction period.
- The project has made it possible to treat sewage water from a densely populated coastal area of Port Moresby City, home to approx. 90,000 people, thus enabling improvements in the marine environment and the sanitary conditions for local residents. The project adopted an activated sludge process (oxidation ditch process), which allows relatively low-cost operation and maintenance, and was the first sewerage system project to which the Special Terms for Economic Partnership (STEP) were applied.
Data
Period:From April 2016 to November 2019
Procuring Entity:Kumul Consolidated Holdings
Applicant:DAI NIPPON CONSTRUCTION
Relevant Companies
Design:NJS CO.,LTD.
Construction:Dai Nippon – Hitachi JV
Evaluation points
- Improvement in ocean pollution also prevents the spread of water-related diseases in the coastal area. Sewage water is treated with ultraviolet rays, not chlorine, and released offshore through an ocean outfall pipe to reduce the impact on the marine environment.
- To reduce the construction and operation costs, the activated sludge process (oxidation ditch process) was adopted as the treatment method. The treatment facility differs in height, and the gravity-based natural flow-down method is used to save energy.
- A piping network was built through the active use of existing pipes and pump stations. The newly installed trunk sewer whose total length is 12 kilometers uses high-density polyethylene pipes (HDPE) having high durability and high corrosion resistance, which helps cut operation costs.
- For the one-year period after the start of operation, Japanese instructors train personnel and engage in technology transfers to ensure that the facility is run stably.
Design, Build, Operate & Maintain and Transfer of Salori Sewage Treatment Plant and related facilities in Allahabad[India]
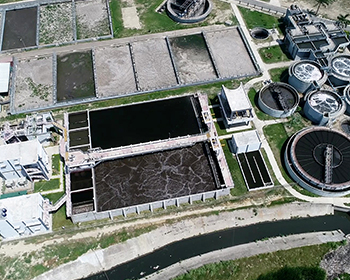
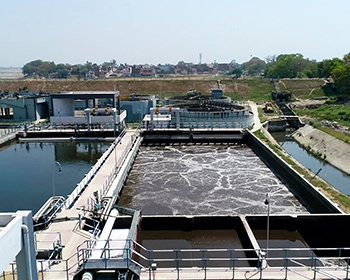
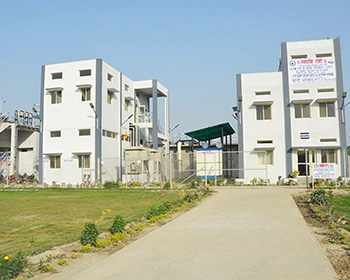
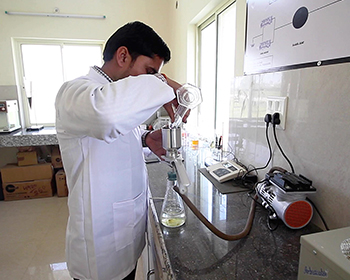
Project overview
- In India, with its extremely serious water issues, the company has worked on the development of sewage treatment facilities, which is at the core of the Ganges purification plan, a national project. Engineers from Japan and India collaboratively completed the infrastructure, winning the recognition of the local government and allowing the company to build a base to continually participate in the project.
- The company received an order for the design and construction of the Salori Sewage Treatment Plant in Allahabad, Uttar Pradesh (with a capacity of 14,000m3/day) and the associated pumping stations as part of the Ganges purification plan promoted by the Government of India, with the project being funded by the World Bank. In addition, the company was entrusted with the 10-year operation and maintenance of the facilities.
- As the treatment method, the company proposed the use of the sequential batch reactor (SBR process), which offers advantages in terms of the required facility area, construction period, and operation costs. The company set out to reduce the risk of any delays to the project while optimizing the lifecycle costs and ensuring the quality of the released water, conforming to the standards set by the Government of India.
- For the design and construction of the plant, the company selected and adopted equipment that can be easily obtained and maintained in India, thus reducing the lifecycle costs. The design and construction of the plant, as well as the O&M activities, have ensured that the plant has been operating smoothly since it started operating in 2016.
Data
Period:From November 2014 to September 2016
Procuring Entity:Uttar Pradesh Jal Nigam, Ganga Pollution Control Unit, Allahabad, Uttar Pradesh
Applicant:Toshiba Infrastructure Systems & Solutions
Relevant Companies
Design, Build, Operation & Maintenance:Toshiba Water Solutions Private Limited
Design Review Consultant:IIT-R(Indian Institute of Technology Roorke)
Evaluation points
- In India, which is particularly prone to serious water issues, the company was able to provide all residences, of both poor and rich, in the target areas with access to a sewage system through the construction of the treatment plant, thus contributing greatly to the improvement of public health across the region.
- The company has a few Japanese engineers stationed in India and is constantly working on human resource development by providing guidance on technologies and know-how to local engineers. The project was completed without cost overruns as the local engineers, trained locally by the company, and stationed Japanese engineers collaboratively imposed stringent controls on the quality, costs, and processes.
- The company strategically set up its base in India by acquiring an Indian company. It gained the recognition of the Government of India and the state government with the completion of this project, and established a base in the country from which it could participate in ongoing projects, including the Ganges purification plan.
National Centre for Infectious Diseases and Centre for Healthcare Innovation[Singapore]
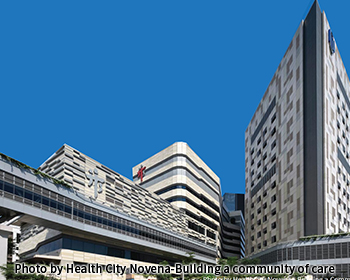
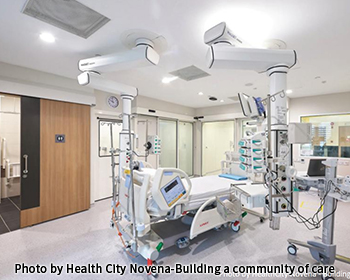
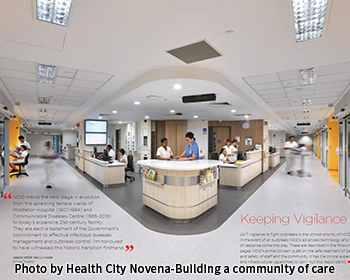
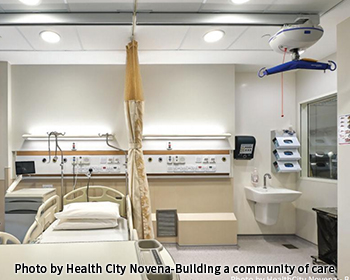
Project overview
- Kajima made full use of BIM to achieve air-tight requirements for the building. In addition, the company realized high standards of safety in unison with stakeholders. Singapore and the UK organizations awarded this project multiple prizes including safety management. In addition, the client and the local community recognized this project with good practices. It contributed to the human resource development of not only Japanese but also multinational staff.
- This site is a healthcare facility within the Health City Novena. It was designed to strengthen Singapore‘s capabilities in infectious disease management and prevention. It functions as a clinical treatment of infectious diseases and outbreak management and also as a research and training facility.
- This is a complex medical facility equipped with negative-pressure patient rooms. The facility has a total floor area of 106,000m2. In addition, 4-basement and multiple connection bridges and tunnels were constructed for connectivity.
Data
Period:From February 2015 to August 2018
Procuring Entity:Ministry of Health, Singapore
Applicant:KAJIMA CORPORATION
Relevant Companies
Design:CPG Consultants Pte. Ltd.
Construction:Kajima Overseas Asia (Singapore) Pte. Ltd.
Evaluation points
- The Kajima’s medical facility design team reviewed the original design and advised the construction department. The proposal to improve the airtight compartment contributed to speeding up the airtightness test and improving reliability.
- At the tender, a structural alternative to shorten the construction period was proposed with engineering assessment. They proposed to shorten the total construction period by 4.5 months and completed this project on time.
- Well coordinated with stakeholders in various fields such as process control, quality management, safety management, and BIM. Received awards related to productivity improvement such as safety management excellence award, excellent building award, and BIM.
- They have prevented delays in the facility opening as well as completion by adopting the requests of medical professionals in advance. In working with the stake-holders, they used digital mockups, including medical devices, to capture the needs of healthcare professionals.
Jakarta Mass Rapid Transit System (North-South Line) Project (Phase 1)[Indonesia]
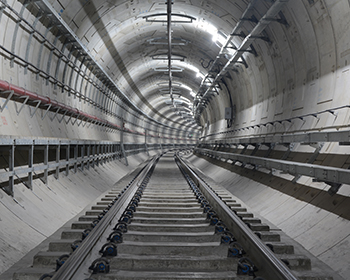
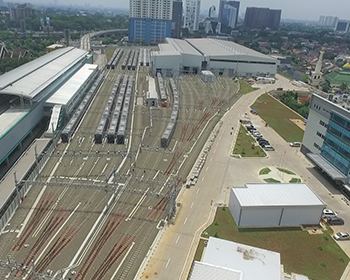
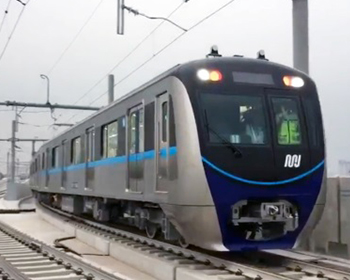
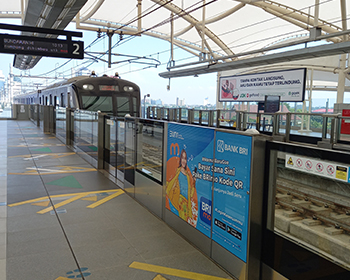
Project overview
- This was a yen-loan-financed project agreed by the governments of Japan and Indonesia to which the Special Terms for Economic Partnership (STEP) were applied. It is the first subway construction project in Indonesia carried out using Japan's outstanding technology and know-how for the purpose of technical transfer from Japan to Indonesia. The subway has eased traffic congestion in the metropolitan area of Jakarta, significantly contributing to the economic development of Indonesia.
- As the first mass rapid transit (MRT) system built in Indonesia, the railway line runs over 15.7 km between Bundaran HI Station in the heavily congested central part of Jakarta and Lebak Bulus Station in the southern part.
- In this yen-loan-financed project under the Special Terms for Economic Partnership (STEP), an all-Japan project team engaged in a range of Phases from master planning to construction and O&M support. Joint ventures mainly composed of Japanese companies took charge of the civil and architectural construction works for elevated bridge (approx. 9.8 km), a tunnel (approx. 5.9 km), a total of 13 railway stations, and a depot, as well as the procurement of 96 cars and the introduction of a railway system, through all of the construction pakages. Of particular note, While six-car trains usually run at intervals of 10 minutes, this system is designed to be able to run trains at five-minute intervals during the commuting hours in the morning and evening.
Data
Period:From August 2013 to March 2019
Procuring Entity:PT.MRT JAKARTA
Applicant:
Oriental Consultants Global Co., Ltd., Japan International Consultants for Transportation Co., Ltd.,
TOKYU CONSTRUCTION CO., LTD., OBAYASHI CORPORATION, SHIMIZU CORPORATION, Sumitomo Mitsui Construction Co., Ltd.
Relevant Companies
Construction supervision:OCG/JIC/Pacific Consultants JV
Construction:
Tokyu Construction JO, Obayashi Corp. JV, Shimizu Corp. JV, Sumitomo Mitsui Construction JV
Others:
OCG/ALMEC JPIJV (master plan), Nippon Koei/Chodai/Japan Electrical Consulting/Koken Architects JV (basic design), JIC/ Nippon Koei/ OCG/PADECO JV (O&M support), Sumitomo Corp. and Nippon Sharyo Ltd. (Procurement of Rolling Stock), etc.
Evaluation points
- This first subway construction project in Indonesia was carried out by an all-Japan project team made up of Japanese companies. The subway has eased traffic congestion in the capital of Jakarta, significantly contributing to the economic development of Indonesia. This project offers a good example of Japan‘s success model implemented overseas, which is characterized by a shift to a transportation system centering on railway construction and a combination of railway construction and development of areas along railway.
- Each station has all possible measures in place against earthquakes, fires, and floods, based on Japan's disaster prevention measures.
- The rolling stock adopts lightweight car bodies, one of Japan‘s strengths, thus optimizing the design of the civil structure and reducing costs, among other things. This project succeeded in exporting Japan‘s high-quality railway infrastructure technology as an entire system.
- Many Indonesian workers were employed for the construction works, actively promoting the technical transfer. A stable O&M framework, including troubleshooting, has been established through technical assistance and transfer from Japan.
Maintenance and Rehabilitation Project of First and Second Bosphorus Bridge[Turkey]
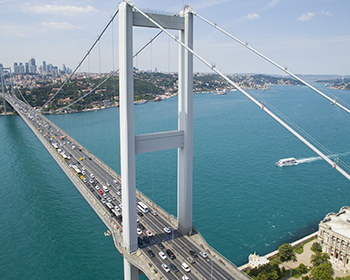
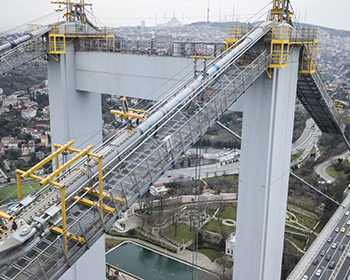
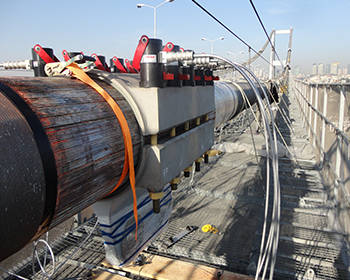
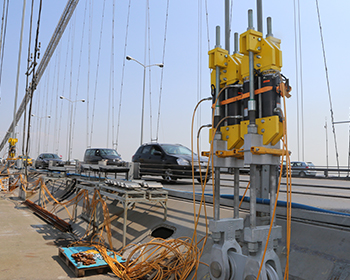
Project overview
- IHI Infrastructure Systems Co., Ltd. has conducted large-scale repair work of the First Bosphorus Bridge (span length of 1,074 m; completed in 1973; constructed by a British company) and Second Bosphorus Bridge (span length of 1,090 m; completed in 1988; constructed by the applicant), which connect the Asian and European sides of Turkey.
- First Bosphorus Bridge was deteriorated due to its age, and therefore they replaced all the 240 diagonal hangers with vertical hangers. This kind of replacement work was the first attempt in construction history, and they were able to complete the work without the full traffic closure. This work was carried based on a recent research, which proves that diagonal hangers tend to inflict greater damage on the bridge girders than vertical hangers.
- To reinforce the suspension bridge’s main cables, they used reinforcement strands, and this process was almost unprecedented. At the same time, they implemented preventive maintenance by installing dehumidifiers and an automatic humidity control system to prolong the life of the suspension bridge at a lower cost.
Data
Period:From December 2013 to March 2019
Procuring Entity:General Directorate of Highways (Republic of Turkey)
Applicant:IHI Infrastructure Systems Co., Ltd.
Relevant Companies
Design:Parsons Transportation Group Inc.
Construction:IHI Infrastructure Systems Co., Ltd. Mak-Yol Construction Industry Tourism and Trading Co. Inc. JV
Evaluation points
- 40 years have passed since the construction of First Bosphorus Bridge (25 years for the Second Bosphorus Bridge) and for this reason, the initial traffic capacities of these bridges were over exceeded up to the level where restriction on heavy vehicles were necessary. They have successfully achieved in reinforcing these two bridges with the unique technologies, which also resulted in decrease of cost.
- Their past maintenance experience and achievements in Turkey, which include the “First Bosphorus Bridge Soundness Evaluation Project” and “Seismic-Reinforcement Project on Second Bosphorus Bridge and Large Scale Bridges in Istanbul” were highly evaluated in Turkey, and therefore they were able to be awarded as a contractor of this project as well.
- The demand of maintenance and reinforcement work of large scale bridges is keep growing in both Japan and Turkey, hence, they have been putting great efforts on acquiring know-hows on maintenance work and developing skills of young engineers for the purpose of fulfilling these demands.
Noguchi Advanced Research Laboratories[Ghana]
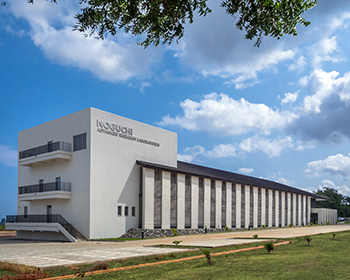
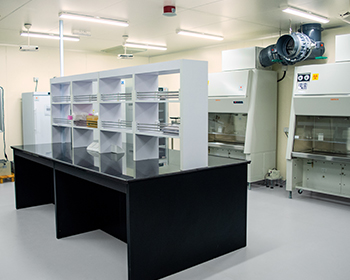
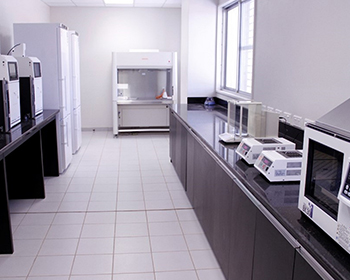
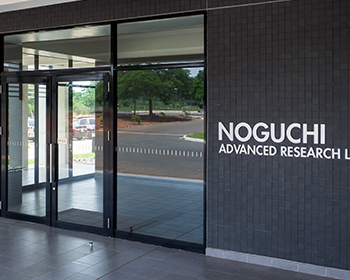
Project overview
- This project involved the construction of a medical research institute with state-of-the-art research facilities in Ghana, West Africa. This country has close ties with Dr. Hideyo Noguchi. During the current COVID-19 crisis, the institute has also been playing a key role in research into infectious disease control in the local community, thus making a major contribution to society as a whole.
- Within the Noguchi Memorial Institute for Medical Research, which was established in 1979 using Japanese ODA, a cutting-edge infectious disease research center devoting itself mainly to infectious disease research was constructed through the grant ODA project. This newly constructed research center is equipped with BSL3 laboratories, PCR laboratories, and laboratories dedicated to immunology, virology, and bacteriology.
- In this area, with its hot and humid climate and frequent dusty seasonal winds, high-quality supervision and administration were applied during the construction phase, by establishing procedures involving the installation of high-performance HEPA filters for the construction, and carefully checking workers’ entering to and exiting from the laboratory.
- The laboratories have acted as an international base for countering the novel coronavirus infections in West Africa, conducting 80% of the medical tests for the infections in Ghana and about 50% of those in countries around West Africa during the initial stages of the spread of the infection around Africa.
Data
Period:From March 2017 to September 2018
Procuring Entity:Noguchi Memorial Institute for Medical Research, University of Ghana
Applicant:SHIMIZU CORPORATION
Relevant Companies
Design:NIHON SEKKEI, INC.
Construction:SHIMIZU CORPORATION
Evaluation points
- The application of laboratory design and construction technologies, developed by Japanese companies inside and outside the country, has contributed to the provision of a quality infrastructure.
- Japanese technologies were applied—as an example, the BSL3 laboratories where precise air conditioning control is required were constructed with procurement from Japanese companies. In the selection of materials, not only initial cost but also quality, ease of maintenance, and the degree of aftercare services were considered prior to the implementation of the procurement plan. Japanese staff were on site from importation to installation while attention was given to ensure that no problem would occur after the start of the operation through the continuous provision of aftercare services.
Tank Hill Park with Yamasen Japanese Restaurant[Uganda]
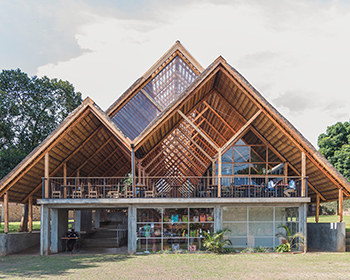
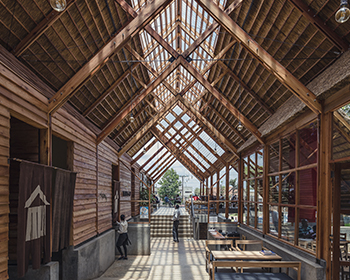
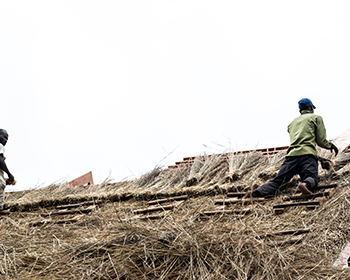
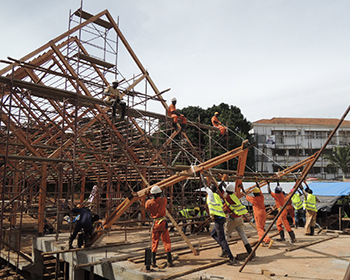
Project overview
- This was the first project in Uganda in which a Japanese company had been responsible for all the activities from construction to operation, using only funds from the private sector. Although they did not have enough materials or human resources and had only a limited budget, TERRAIN architects and Cots Cots were able to successfully transfer Japanese technology to complete the construction of a commercial facility that local people hold in high regard.
- This project involved planning, designing, and constructing of a complex commercial facility with Japanese restaurants and other tenants in Kampala, the capital of Uganda, a landlocked country in East Africa.
Site area: 3,371m2
Total floor area: 785m2
Structure: Mixed construction using wood and reinforced concrete - They successfully used eucalyptus wood, the cheapest and most versatile material in the area, as a structural and finishing material by carefully drying and treating it. They also used materials and building methods that are native to the area such as a thatched roof and fired bricks.
Data
Period:From January 2017 to August 2018
Procuring Entity:Cots Cots Ltd.
Applicant:TERRAIN architects, Cots Cots Ltd.
Relevant Companies
Design:TERRAIN architects
Construction:Cots Cots Ltd. TERRAIN architects
Local architect:Dream Architects
Evaluation points
- While it is common for an overseas workforce and imported building materials to be used in large-scale projects, for this project they employed only one Japanese staff member. The remainder were all local people. The materials were procured locally as far as possible. Additionally, although eucalyptus wood is not normally used as a structural material despite its low cost and abundance, they were able to use it as a structural material by applying the wooden building techniques traditionally used in Japan.
- This facility is now held in high regard by both local and foreign people as an accessible facility where they can easily get together, despite it typically being difficult for foreigners and locals to mix in Africa. Since this facility was provided for common use, it has given opportunities for a Japanese restaurant and other tenants to utilize local ingredients and human resources and for a nursery established in the facility to help develop an environment where females raising children can comfortably use the facility or work, supporting continuous development in the area. In addition, this facility, including a tenant Japanese restaurant operated by the first Japanese chef in Uganda, is also working as a base for promoting Japanese culture.