5th Japan Construction International Award
Construction Project Category
- East-West Road Improvement Project (N-70)[Pakistan]
- MRT Downtown Line 3; Bedok North Station, Mattar Station, Bencoolen Station and Associated Tunnels[Singapore]
- The Project for Construction of New Thaketa Bridge[Myanmar]
- Three Runway System Project C3201 - Deep Cement Mixing Works (Package 1)[Hong Kong Special Administrative Region]

East-West Road Improvement Project (N-70)[Pakistan]
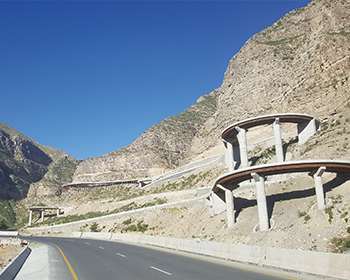
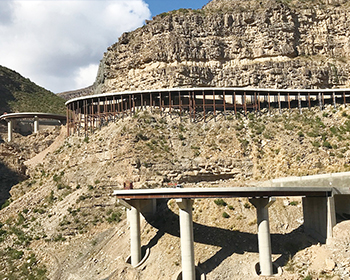
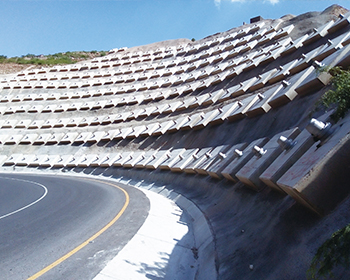
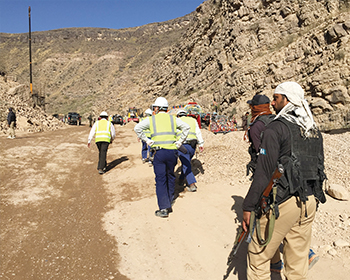
Project overview
- National Highway No. 70, one of the few major highways through the mountainous regions of Pakistan, has a series of narrow, zigzag sections with frequent falling rocks and landslides that often stop the flow of traffic. In this project, the construction work was carried out while maintaining the flow of traffic, strengthening the highway‘s resilience to natural disasters while simultaneously enhancing its capacity.
- The project was located in the steep mountainous area with a height difference of 600 m, and the project improved the 11.5km road with an earthwork section, including two zigzag areas, and a bridge section. It drastically modified the road alignment to improve travelability. With the average longitudinal slope limited to 4.6%, vehicles can now pass on both sides of the road with the speed limit of 40 km/h through all the sections (except the sharp curve sections for which the speed limit is 30 km/h). Newly constructed 11 bridges, including a 4-span continuous steel box girder bridge with a minimum radius of 30 m at the sharp curve sections, improved the road travelability for longer vehicles.
- Proactively utilizing Japanese technology for the first time in Pakistan, The construction was carried out without obstructing the flow of traffic. It adopted Pre-fabricated steel widening bridge in the steep zigzag segments in parallel with existing roads and introduced Mechanical stabilized earth retaining wall construction and Foamed cement banking method for the banking sections.
- Meanwhile, the project proactively adopted existing methods using locally quarried stone. It successfully reduced costs and created jobs in the region by effectively combining the advantages of Japanese engineering and local construction methods.
Data
Period:From July 2016 to December 2019
The Employer:NHA:National Highway Authority
Applicant:TAISEI CORPORATION / CTI Engineering International Co., Ltd.
Relevant Companies
Design:CTI Engineering International Co., Ltd. / Oriental Consultants Co., LTD.
Construction:TAISEI CORPORATION
Evaluation points
- By adopting Japanese technologies such as weather-resistant steel for steel bridges and epoxy-coated ECF strands for the ground anchors, life cycle cost reductions were achieved.
- The project obtained the cooperation of Japanese specialized construction companies for work requiring technological know-how such as pipe driving into hard bedrock. Meanwhile, the Japanese engineers transferred their know-how of the maintenance and management of roads to the local engineers by creating manuals covering inspection and repair.The project obtained the cooperation of Japanese specialized construction companies for work requiring technological know-how such as pipe driving into hard bedrock. Meanwhile, the Japanese engineers transferred their know-how of the maintenance and management of roads to the local engineers by creating manuals covering inspection and repair.
- The project strengthened disaster-prevention measures and the highway's resilience to natural disasters by establishing rockfall protection walls and new drainage channels while also implementing other effective actions for sections where traffic was often obstructed due to falling rocks, landslides, and flood.
- The construction work was carried out throughout the project while maintaining the flow of traffic. The project successfully minimized the negative impact of the construction work on the local economy, contributing to the maintenance of convenience for local residents.
MRT Downtown Line 3; Bedok North Station, Mattar Station, Bencoolen Station and Associated Tunnels[Singapore]
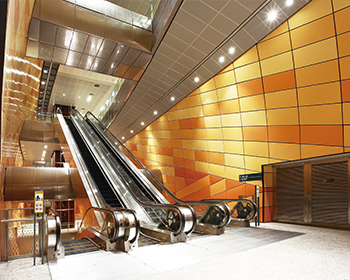
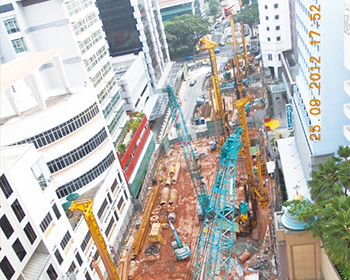
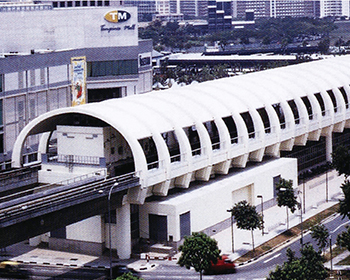
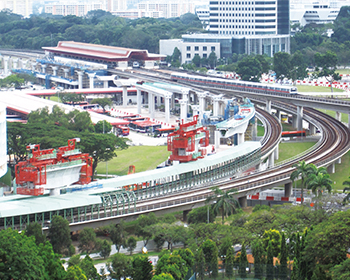
Project overview
- For subway construction projects in Singapore, the company has completed three technologically difficult construction packages safely and within the contract period, which involved deep excavation in an urban area, tunnelling by Tunnel boring machine (TBM) under complicated soil conditions, and large-scale excavation in a residential area, thereby demonstrated our technological capabilities as a Japanese company and also contributed to the development of public transport infrastructures.
- Bencoolen Station, with six basement levels and total floor area of 24,000 m2, is the deepest station with the largest floor area in Singapore. Construction of the station was difficult due to gigantic boulders in the ground. The works was completed in a limited space surrounded with numerous commercial buildings and respecting intentions of the stakeholders.
- Mattar Station and Tunnels is to construct an underground station and tunnels by TBM with a total length of 2.7 km (for both inner and outer bound). Boring of the tunnels were difficult due to complicated but predominantly soft ground, passing through sections where the linearity distance between inner and outer tunnel being only 1 D or less and proximately an existing main sewerage.
- Bedok North Station and Tunnels is to construct an underground station and tunnels by TBM with a total length of 1.4 km (for both bounds). The underground station has a special explosion-proof structure where required, so that the entire station can serve as a shelter in emergencies. The structure has thicker outer walls with more reinforcing steel to provide a greater degree of safety for the people.
Data
Period:From February 2011 to December 2016
Procuring Entity:Land Transport Authoirty
Applicant:SATO KOGYO CO., LTD.
Relevant Companies
Design:ARUP, T.Y. Lin International / Aedas, ONG & ONG
Construction:SATO KOGYO (S) PTE. LTD.
Evaluation points
- For excavation of boulders and tunneling, customized machineries in cooperation with a Japanese construction machinery manufacturer and TBMs from Japanese manufacture have been deployed respectively. The Company has applied Japanese technologies in both intangible and tangible ways, and completed the projects in collaboration with a local partner companies.
- The applicant has continued to secure contracts for MRT line construction projects in Singapore. The proposal for assigning local staffs who have been trained locally is among the important factor to secure the contracts. Because the results of this projects were highly evaluated, the Company also won Singapore‘s first large-diameter tunnel construction contract for a new Terminal 5 of Changi International Airport.
- The Company has received a numerous local awards, such as the Construction Excellence Award in the Civil Engineering Business Division by Building and Construction Authority, the Land Transport Authority Infrastructure Best Partner Award by Land Transport Authority, and the Safety Award of the Workplace Safety and Health Council of the Ministry of Manpower. The Company has positively conducted public relations activities in Singapore by, for example, announcing their accomplishments in newspaper advertisements, thereby appealing Japanese technological capabilities.
The Project for Construction of New Thaketa Bridge[Myanmar]
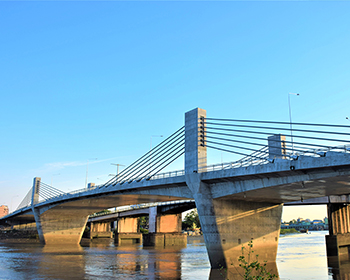
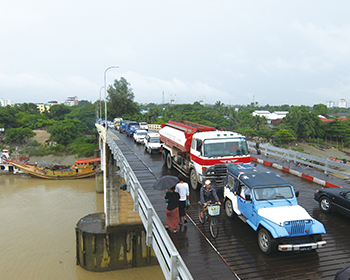
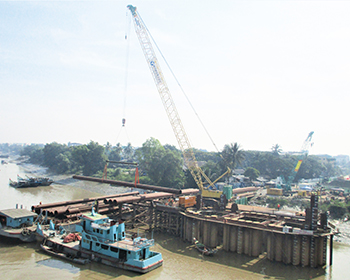
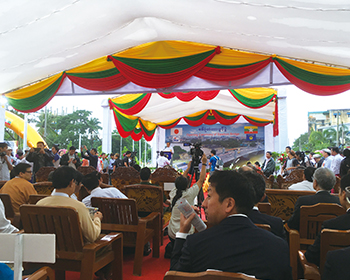
Project overview
- The construction of Baluchaung No. 2 Hydropower Plant commenced in 1954 as a first project under Japan‘s economic cooperation for Myanmar. Since then, various types of cooperation have been provided for developing the country. The New Thaketa Bridge was built under the Japanese grant aid as one of the cooperation. The new bridge has accelerated the development of the country not only by improving traffic situation and safety but also by transferring advanced technologies to local engineers during its construction.
- The existing Thaketa Bridge had a key role for logistics as it connects the city center of Yangon to the special economic zone (SEZ) located in the south part of the city. However, the existing bridge has been in service for about 60years with severe traffic congestion. The damage accumulation caused serious degradation in the bridge. With the aim of overcoming such circumstance, the construction of a new bridge was determined under Japanese grant aid.
- For the bridge piers in Pazundaung Creek, steel pipe sheet pile foundation was adopted for the first time in Myanmar. Shop-fabricated long steel pipe sheet piles were procured to the construction site by water-transport without cutting in manufacturing factory. As this way of procurement made the construction process simple and more reasonable, the construction schedule was well-controlled regardless of the weather while prioritizing the quality assurance.
- It is important to select a suitable bridge type to accommodate busy water traffic on Pazundaung Creek. The PC extradosed bridge was adopted to efficiently secure the clearance required for shipping lanes by setting the space between piers and the height from water level to girder in proper way. Applying this bridge type was also the first attempt in Myanmar.
Data
Period:From April 2015 to July 2018
Procuring Entity:Ministry of Construction, The Republic of the Union of Myanmar
Applicant:Nippon Koei Co., Ltd. / TOKYU CONSTRUCTION CO., LTD. /
TOYO CONSTRUCTION CO., LTD. / IHI Construction Service Co., Ltd.
Relevant Companies
Design:Nippon Koei Co., Ltd.
Construction:TOKYU CONSTRUCTION CO., LTD. /
TOYO CONSTRUCTION CO., LTD. / IHI Construction Service Co., Ltd.
Evaluation points
- The new bridge are safe and secure because of its smooth road alignment and wider width. The massive structure alleviates the weight limitation and the 4-lane road considerably reduced chronical traffic congestion. It promotes economic activity more and more by enhancing the logistics capability.
- This project contributed to the inprovement of the technical skills of engineers in Myanmar by implementing technical transfer program and introducing the Japanese technologies such as steel pipe sheet pile foundation and PC extradosed bridge.
- At the opening ceremony, the Construction Minister of Myanmar gave a compliment for the quality of the new bridge, which was built under the quality control in Japanese level. The project associated with the new bridge construction started immediately after the relaxation of the restrictions on foreign investment. The success of this project became a foothold for the Japanese construction industry to enter the Myanmar market.
- The burden for maintenance can be reduced by employing cable vibration damping devices which decrease damage on the structure. Maintenance manuals were also well-prepared for reducing the life cycle cost.
Three Runway System Project C3201 - Deep Cement Mixing Works (Package 1) [Hong Kong Special Administrative Region]
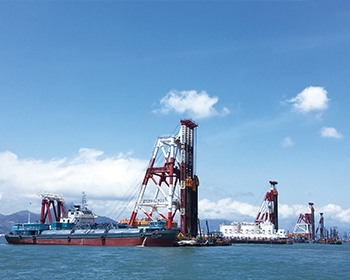
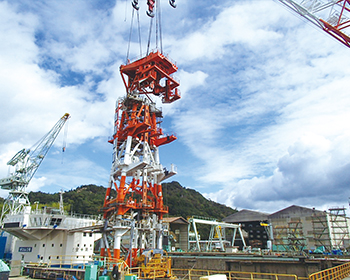
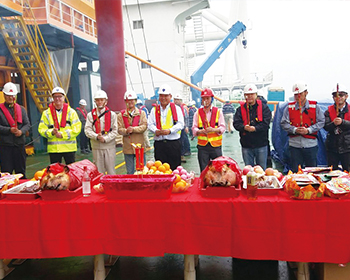
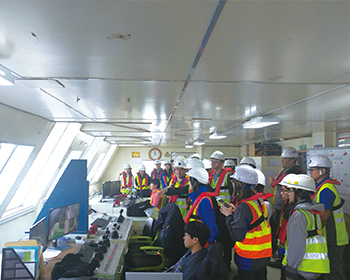
Project overview
- The company carried out large-scale ground improvement work using the Japanese Cement Deep Mixing (CDM) method, which was adopted in Hong Kong for the first time. With this construction technique, as well as its approach to safety and the environment being highly evaluated, the company successfully demonstrated Japan’s infrastructure development capability at Hong Kong's main gateway.
- In this project, the company carried out the ground improvement work using the CDM method with 74,074 piles (area of improvement: 4.63 m2 per pile; dimensions: φ1,300 mm x 4 axes) in the 133-hectare work area (650 hectares for the entire area for which the construction of the third runway was planned). The improved volume was approximately 7,300,000 m3, due to the application of the large-scale CDM method.
- Part of the work area was used as a pit to dispose of construction waste soil. To provide water pollution control measures against any outflow of contaminated water from the construction waste soil or the outflow of cement slurry during the construction work, 11 CDM improvement vessels, a real-time water quality measuring device, a pollution control frame (primary barrier), and silt fences (secondary barrier) were utilized during the construction work.
- The area of the construction was adjacent to an active international airport; therefore, the construction work was carried out under Airport Height Restriction. Before the CDM improvement vessels were transported to Hong Kong, the height of the scaffolding on them was lowered (so that the height from the water surface to the highest point was no more than 50 m). The construction work was carried out with the position of all the vessels engaged in the work and their heights being monitored on a real-time basis.
Data
Period:From August 2016 to August 2019
Procuring Entity:Airport Authority Hong Kong
Applicant:PENTA-OCEAN CONSTRUCTION CO., LTD. (Representative of Penta-Ocean - China State - Dong Ah Joint Venture)
Relevant Companies
Design:Atkins / Mott Macdonaid
Construction:Penta-Ocean – China State – Dong Ah Joint Venture
Evaluation points
- The CDM method enables the rapid implementation of ground improvement work, solidifying soft ground in situ by agitation and mixing with cement slurry. Each area where this part of the work was finished was handed off to the subsequent reclamation work, contributing to the smooth progress of the runway construction project.
- The company was responsible for the CDM Trial Works in 2012 and 2015, an upstream phase of this project, and contributed to the success of the work. After establishing the company structure leveraging the knowledge, know-how, and human resources obtained from the CDM test construction work, it participated in the bidding process and won the order for Hong Kong’s first large-scale CDM construction work.
- The company carried out the construction work while considering the surrounding environment by observing the ecology of Indo-Pacific humpback dolphins, taking measures to reduce the noise produced by the CDM vessels, installing dust collectors on the cement silos, and taking other similar measures. It also ensured that advance evacuation was completed when a typhoon was forecast, preventing maritime and dredging anchor accidents. Thanks to these efforts being highly evaluated, the company received multiple environmental and safety awards from the Airport Authority Hong Kong and the Hong Kong Government.
- The company also accepted interns from Japanese universities and introduced younger officials of the Airport Authority Hong Kong and the Hong Kong Government to the CDM method and state-of-the-art machinery through site visits, contributing to the development of young talented individuals.